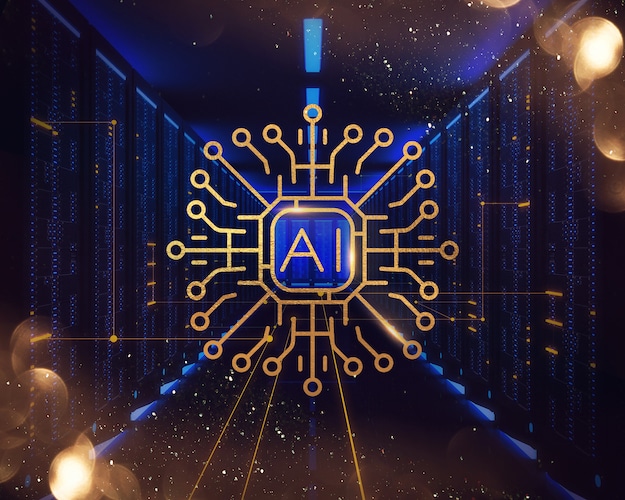
[ad_1]
When you are into production, especially giga-scale and mega-scale production, you need sharp visuals and a lightning speed of screening to prevent damaged devices from reaching your customers
SixSense has developed a no-code platform for building, monitoring, and maintaining deep learning models for computer vision applications. Currently, production engineers utilise the platform to create AI models that can detect and classify defects in photos. They are shifting from a decade-old inspection process based on manual labour or rule based systems to a significantly more efficient and scalable AI based solution using the SixSense AI platform.
What happens when there are multiple inaccurate inspections |
• Cost of labour increases |
Visual quality inspection is one of the most critical processes in manufacturing and is used to control the cost of quality. In a 24/7 production line, visual checks that happen increase the cost of quality exponentially. Today, inspections have a very high error rate of up to 40%. Manufacturers generally have a team of operators, who might make mistakes due to factors such as fatigue or oversight.
Sometimes, engineers automate their processes using rule based algorithms. But they fail to scale and adapt to a broader catalogue with subtle variations between defect classes. This leads to defects getting missed or false alarms.
How does ClassifAI work? |
• You can upload and label large volumes of data in a matter of seconds |
“We have identified this problem and have built an accurate AI-powered automatic defect classification software called ClassifAI,” says Akanksha Jagwani, Co-Founder & CEO at SixSense.ai. “Our technology integrates with existing image capture tools, analyses at a very high speed, and classifies the defect into various categories. The AI monitors and maintains itself and ultimately writes back the class codes of the defects for decision making.” This software is able to take any kind of image data—optical, SEM, X-Ray, etc—and analyse it for accurate defect classification.
[ad_2]
Source link